Engineer Walter Curlook was ‘Pied Piper of productivity’
Engineer Walter Curlook was ‘Pied Piper of productivity’
Walter Curlook’s favourite film was the Danish drama Babette’s Feast. Perhaps this story, of a Parisian chef who takes refuge in an austere religious community, then spends all her money to prepare a sumptuous meal that awakens her hosts’ repressed senses, confirmed Mr. Curlook’s belief in generosity – sharing wealth to enlarge people’s horizons.
As a metallurgist, engineer and manager who spent his entire career as an executive at Inco when it was the world’s largest nickel miner, he understood how to create wealth as well as share it. Mr. Curlook, who died on Oct. 3 in Toronto of a brain hemorrhage at the age of 85, held 14 patents for improvements to nickel refining and played a role in the establishment of a science centre, a college and a research facility for particle physics in Sudbury that has no equal in Canada.
Brilliant and tenacious, he never stopped working. After he retired from Inco, he became an adjunct professor in materials science and engineering (unpaid) at the University of Toronto and donated $1-million to set up two laboratories there for the study of minerals.
“He was one of those people able to use a larger percentage of his brain than most of us,” his son Michael said. His daughter Christine Stinson recalled her father’s ability to be so absorbed in some problem that he would not hear his children speak: “He would sort of zone out and my mother would tell us, ‘Quiet – your father is thinking.’”
In the 1970s, Sudbury’s smelters belched thousands of tonnes of sulphur dioxide into the atmosphere daily, killing vegetation and poisoning surrounding lakes. Mr. Curlook’s most important contribution might have been overseeing Inco’s $650-million pollution-abatement program that ended with the air clean, new trees planted and northern grasses growing over slag heaps.
He was born with a nickel-plated spoon in his mouth on March 14, 1929, in Coniston, Ont., near Sudbury, one of five children. His father, William Curlook, was a Ukrainian-born nickel miner, working in feudal conditions; his mother, Stephanie (née Acker), was a disciplined woman of German/Ukrainian extraction.
Money was short, so Walter obtained part-time work at Inco from the age of 15 until his graduation. At 17, on full scholarship, he left for the University of Toronto, where he earned a clutch of degrees in science and engineering.
In 1953, PhD in hand, he took up a postdoctoral fellowship at the Nuffield research lab of London’s Imperial College of Science and Technology, an institution that had specialized in Earth sciences since the mid-19th century.
At 18, he met Jennifer Burak, then 15, at a Catholic youth dance in Toronto. He did not see her again until five years later, when sparks flew. Their wedding was postponed until the groom returned from London.
Hired at 25 by Inco as a metallurgist at the Copper Cliff mine, he returned with Jennifer to Ontario’s mining country. Mr. Curlook’s research and innovation skills led to rapid promotion, first to supervisor of the research station at Port Colborne, then back to Copper Cliff as research superintendent in 1964.
Nickel is the fifth most common element on Earth and is used in thousands of products; because it’s non-corrosive, 65 per cent of what is mined goes into making stainless steel. Nickel naturally clings so stubbornly to other minerals – including cobalt, copper, sulfides and iron – that it takes powerful furnaces and heavy industrial equipment to crush, blast, pulverize, roast, melt and leach it into a state called nickel matte – still impure, but ready for sale.
The aim of the research teams Mr. Curlook headed was to find better ways to produce nickel matte and to find uses and markets for other minerals that were separated out.
In 1969, he went to Paris to negotiate with the French government enterprise COFIMPAC for the rights to exploit rich nickel deposits in New Caledonia, east of Australia. He and the family lived in Paris for three years, exploring France on weekends in their small Peugeot. “My father loved French culture,” Ms. Stinson recalls.
In the end, though, Mr. Curlook was stymied by French bureaucracy and the contracts he sought went to other parties.
The Goro deposit, former colleague Sam Marcuson says, “was like a beautiful woman he wanted to marry. She turned him down but he never forgot about her, and kept after her.”
Two decades later, after the other parties failed to deliver, Inco approached the French government again. Mr. Curlook moved with his wife to New Caledonia for three years and obtained the necessary permits for the startup of Goro Nickel, owned 85 per cent by Inco, 15 per cent by the French. Nickel production at Goro finally started in 2010.
Following the Paris years and another stint at Copper Cliff, Mr. Curlook moved his family to New Jersey from where he took the train daily to work at Inco headquarters in Manhattan from 1974 to 1977 as a vice-president of the company.
When headquarters moved to Toronto, the family moved there. Mr. Curlook became president and CEO of Inco Metals, a unit of Inco, and in 1984 set up Continuous Mining Systems Ltd. in Sudbury, a subsidiary manufacturing mining equipment. As well as chairman of Continuous Mining, he was president (later chairman) of Inco Gold, yet another Inco unit. In 1989, he was appointed a director of Inco and was also president commissioner of PT Inco in Indonesia.
The 1980s were difficult. While Inco was still recovering from the nine-month-long miners’ strike of 1978, the worldwide price for nickel dropped from about $3 a pound to $1.41. (It now hovers around $7.) Inco closed its least-efficient refinery, at Port Colborne, Ont., and consolidated operations at Copper Cliff and and Thompson, Man.
Mr. Curlook’s commitment to research paid off in increased productivity for a reduced work force. He introduced generous bonuses for anyone with a good idea to improve efficiency. The Globe hailed him as “the Pied Piper of productivity” in a 1985 article.
In the early 1980s he was part of a group of Inco executives who started Science North in Sudbury; Inco donated $5-million for capital costs. David Pearson, the facility’s founding director, recalls that Mr. Curlook was “very supportive of what the science centre might do to encourage children along the path of innovation and achievement he had followed.”
He also supported setting up Cambrian College and the Sudbury Neutrino Observatory (SNO), one of only a handful in the world, which he made sure was given space deep within Inco’s Creighton Mine.
Neutrinos are neutral subatomic particles that cannot be found and studied above ground due to interference from cosmic rays. George Ewan, professor at Queen’s University, was among the physicists who visited various mines in 1983 to find a place for the proposed neutrino experiment. “Walter was very keen to see the experiment there – the decision on the Creighton mine had to go through him,” recalls Prof. Ewan, who is now retired. “He invited us to make a presentation to the directors of Inco. He also had to explain to the people in the village and the mine what we were doing. At all stages, he was a tremendous help. He tried to see the future.”
That first experiment at the SNO solved a long-standing problem in neutrino physics and may yet win a Nobel prize.
Inco had attempted to reduce the pollution caused by its refineries as early at 1972, when it built its Superstack in Sudbury, which sent sulphur dioxide gases high up in the atmosphere. This had the effect of releasing fewer toxins over Sudbury but more throughout the region. Starting in 1988, government regulations and public opinion forced Inco to undertake a serious sulphur dioxide abatement and regreening program, under Mr. Curlook’s management.
“Abatement work was a team effort,” Mr. Marcuson explained. “It was done by shutting down the old reverberatory furnaces, building two flash furnaces, building two acid plants and creating a new process for treating copper.”
In 1985, Inco’s plants released 685,000 tonnes of sulphur dioxide annually. The emissions were down to 265,000 tonnes by 1994 – the year that Mr. Curlook retired, continuing as a consultant.
In his late seventies, he oversaw the construction of a nickel refinery for CVMR Corp., a Canadian mining company.
“He worked for us from 2005 to 2008, on the Jilin project [in China],” recalls Kamran Khozan, chairman and CEO of CVMR, in a phone interview. “We designed and engineered it in Canada, manufactured the parts and shipped it from here. It had to be assembled like Lego. Walter got the job done, under hostile conditions. His knowledge was not matched by anybody in the field.”
Walter Curlook also played the violin and the piano, was a champion blueberry picker and collected the art of Jamie Wyeth and Alex Colville. “He was not just a left-brain kind of guy,” his son Michael says.
Among his many honours were an Order of Canada, two honorary degrees and induction into the Canadian Mining Hall of Fame.
He leaves his wife, Jennifer Curlook; sons, Michael and Paul; daughters, Christine and Andrea; sisters, Jenny and Mary; and five grandchildren.
To submit an I Remember: [email protected]
Send us a memory of someone we have recently profiled on the Obituaries page. Please include I Remember in the subject field.
Source from Global and Mail
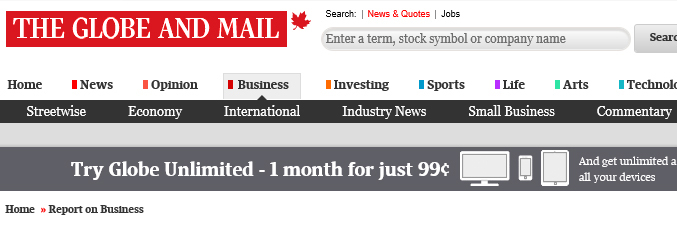
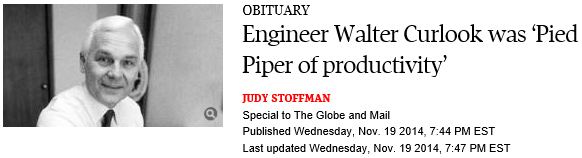
Read also